SR HNA-HNA-25-1402
2025年6月,GCAM定检中检查发现,多架飞机左主轮舱隐蔽区域的起落架传感器下位锁线束与扰流板控制液压管间隙较小,产生干涉,存在磨损超标情况。
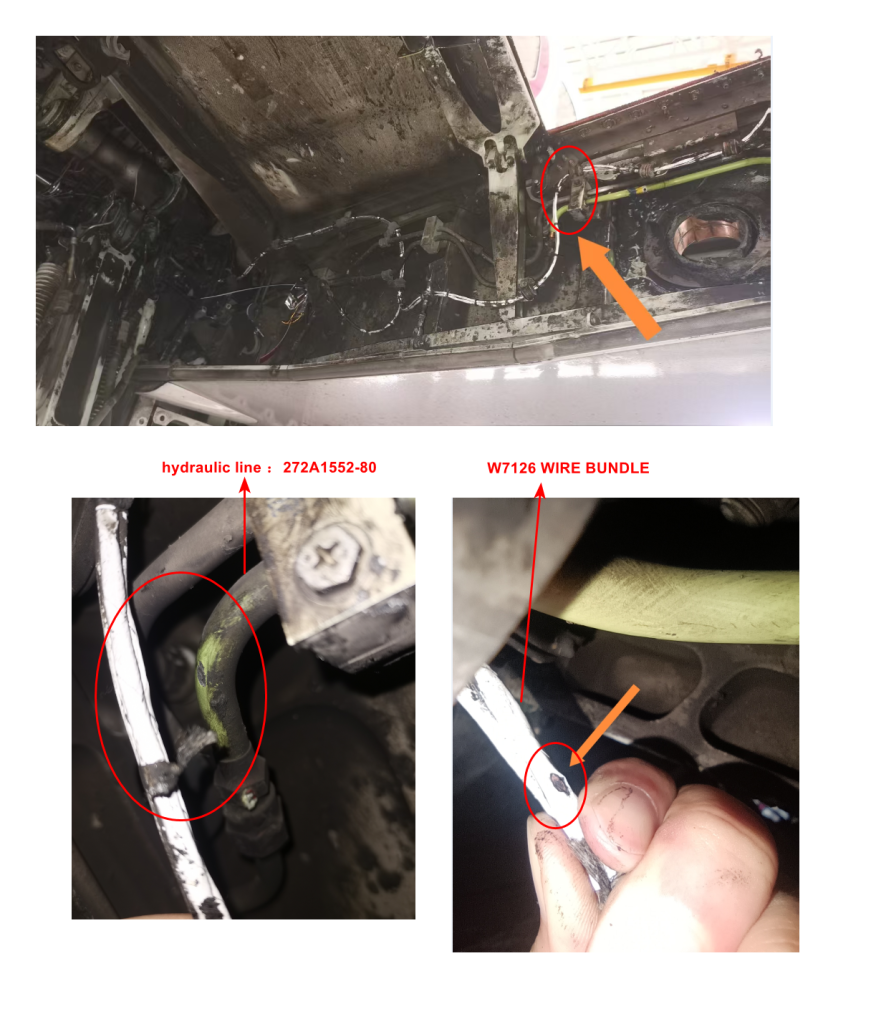
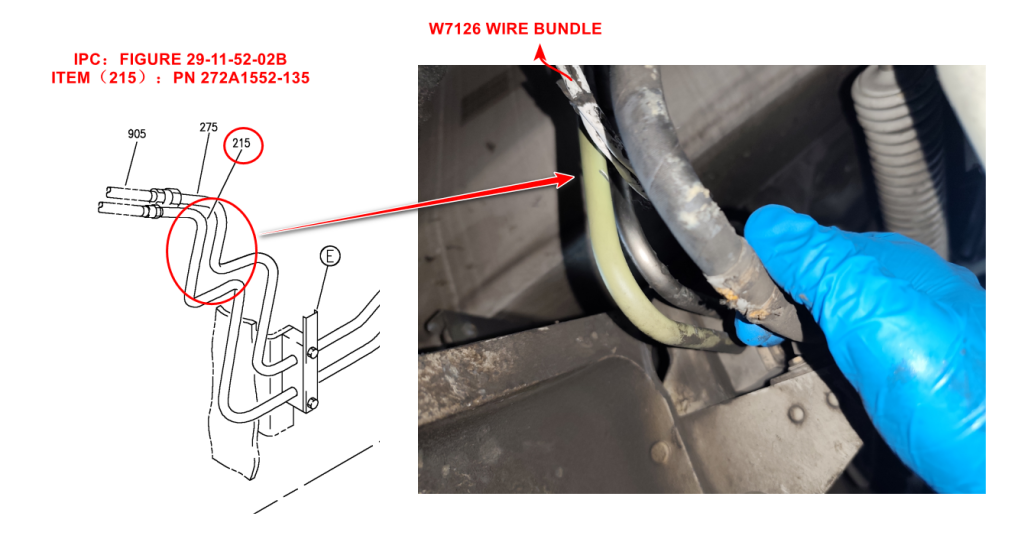
管路件号272A1552-80和 272A1552-135 TUBE ASSY-B RETURN SPOILER 为B系统的扰流板回油管。建议:
- 将识别到的风险点加入定期检查中,缓慢消化。
- 跟踪GCAM发的SR的波音后续答复,如何彻底避免。
- 向航材提备件需求。
SR HNA-HNA-25-1402
2025年6月,GCAM定检中检查发现,多架飞机左主轮舱隐蔽区域的起落架传感器下位锁线束与扰流板控制液压管间隙较小,产生干涉,存在磨损超标情况。
管路件号272A1552-80和 272A1552-135 TUBE ASSY-B RETURN SPOILER 为B系统的扰流板回油管。建议:
HNA-HNA-25-0893
2025年近期,由于安监把全航段的发动机振动值参数纳入监控,且不做延时处理,导致多台发动机出振动值超过3的警告,而厂家监控和机上读取振动值均正常。在对几台发动机执行高振动检查后,孔探、磁堵、指示均无异常。总结其高振动特征为:
1,均发生在高原机场;
2,均出现在启动阶段,达到高原启动峰值后,70多N2开始回落到慢车稳定的时候。
3,有时候仅触发HPC,有时候是HPC+HPT,低压段振动值均低。
4,慢车稳定后,发动机全航段振动值正常。AVM自检无信息,振动值无超3的情况。
5,同台发动机在相同场景下,重复出现的概率高。
典型的数据如下:
回跑的案例如下:
由于该类型问题,具备典型特征,且对发动机无损伤表现,就此和厂家做了沟通。
1、波音感谢Ref /A/的回复,已将其分享给CFM,CFM仅有关于两种振动模式响应的经验: • 第一种模式发生在大约65-75% N2飞行怠速阶段,这是由于高压压气机不平衡造成的。 • 第二种模式发生在起飞时,大约在90-100% N2,这是由于高压涡轮不平衡造成的。 报告的情况更符合第一种振动模式响应,在怠速阶段发生,这可能是高压转子不平衡造成的。
2、进一步追问中,表示完成所有排查均未发现问题,有无排故建议。厂家表示,根据 CFM 的经验,当报告的核心振动高且与第一模式(在 65-75% N2 时)一致时,问题可能是由于高压压气机不平衡引起的。最后,如前一个答案所述,对于真正的发动机高核心振动,机翼上的故障排除能力有限,但识别模式将有助于发动机车间检查。
3、波音和CFM已经审查了Ref /A/消息,并建议,基于迄今为止提供的发动机数据和解释,在启动阶段不需要监控VIB值,在除非显示单元记录的值超过3个单位或记录了需要进一步故障排查的维护消息的情况下,也不需要进行发动机孔探检查和其他检查步骤。CFM同意这种做法,因为在机翼上对真正的发动机高核心振动进行故障排查的能力是有限的。
Boeing and CFM have reviewed the Ref /A/ message and advise that, based on the engine data and explanations provided thus far, it is not necessary monitor the VIB value in start phase and it is not necessary to carry out engine borescope and other check steps unless a value over 3 units as recorded by the display unit or if a maintenance message is recorded prompting further troubleshooting. CFM agrees with this approach as there is limited on wing troubleshooting that can be accomplished for true engine high core vibration.
备注:详细波音沟通过程参见SR HNA-HNA-25-0893
CFM初始阶段直接联系的答复,并未有正面答复,只参考了手册。
SE-57-17-15261
一、背景
2025年6月,有飞机过站反映合肥过站检查三号船型整流罩有一个螺帽,自带保险丝,检查发现左大翼三号船型整流罩上部大翼551GB盖板(115A2714-21)的一个固定连杆(115A2950-85)断裂。
二、基本原理
551GB和651GB位于发动机吊架尾部的固定后缘。
盖板551GB/651GB使用拉杆连接,
170为此次失效的连杆,件号15A2950-85。
针对该问题,扩大看有FIX描述过该问题
在左右内侧固定后缘下部面板的对称位置同时发现了缺失的铆钉头。详细情况请参阅附图。该问题于2016年9月23日在JA807X/YR423(TFH 9070/ TFC 6819)上报告。随后重新安装了新的铆钉。然而,重新安装的铆钉头再次丢失。这一情况发生在重新安装后两个月,即2016年11月26日(TFH 9598/ TFC 7207)。在同一架飞机的左右机翼位置同时出现了相同的情况。因此,在C02 C检(TFH 9973/ TFC 7469)期间进行了进一步详细检查。检查结果如下。详细情况请参阅附图。
左机翼内侧固定后缘下部面板(551GB)
a) 前侧转向节组件(件号:115A2950-85)上部叉耳组件分离。
b) 转向节组件上部螺纹磨损和腐蚀。
右机翼内侧固定后缘下部面板(651GB)
a) 支撑梁组件(件号:115A2759-14)的两个轴承孔扩大。
b) 轴承本身存在松动情况。
Solaseed希望其他运营商提供任何类似的经验。
零部件信息:
转向节组件件号:115A2950-85
支撑梁组件件号:115A2759-14
跟帖
作为2017年2月在东京举行的PDA会议的一项行动事项,全日空(ANA)发布了我们关于这一问题的经验。
全日空在以下机翼后缘结构(围绕相关区域)上经历了相同类型的紧固件丢失和磨损损坏:
件号115A2759-13/-14的梁,(波音公司建议,自2009年10月起,向运营商或MRO发送了(195)梁115A2759Y14和(210)梁115A2759Y13。)
件号115A2750-1的支架,
件号115A2179-6的梁,
件号115A6250-6的偏转控制肋,
件号115A2183-1/-3的锯齿板。
请参阅附件中的飞机数据和损坏细节。所有受影响的飞机均在服务通告SB 737-57-1284/PRR 38275-86之后。
全日空认为,根据服务通告SB 737-57-1284/PRR 38275-86进行的修改无法阻止服务通告SB 737-57-1284背景中讨论的问题,且该问题是一个机队范围内的问题。
我们认为需要针对此问题提供额外的永久解决方案。
如果其他运营商在服务通告/适航性限制(SB/PRR)之后的机翼固定后缘支撑结构上经历了相同类型的损坏,请在FIX ISE-57-17-15261或FTE-57-16009上发布有关您经验的评论。
以下是向波音公司的请求:
当前工程政策
1、MP 57-858-01(左)和MP 57-928-02(右),外部-区域(整体目视检查):后梁到后缘-内侧襟翼的外侧-固定后缘的内侧 -左,周期 6600FC。
2、MP 57-848-01(左)和MP 57-918-02,外部-区域(整体目视检查):大翼后梁到起落架支撑梁, 周期6600FC。
将在MP 57-858-01(左)和MP 57-928-02(右)中加入相关检查要求。
来自民航发动机工作组
一、背景
2015-2024 十年间,全球范围内 AGB 原因导致的 CFM56-7B 发动机空停事件共 34 起,每年事件数量和具体次轮线位原因分布如下。从2020年后的趋势可以看出,随着主要占比L3和L4,随着 AGB 4 号线改装 SB72-0564 和 3 号线改装 SB72-0879 的执行,AGB 空停率趋于稳定。
二、基本原理
CFM56-7B 发动机 AGB 将发动机高压转子的机械能传递给附件(3 号线驱动 EEC 发电机、 6 号线驱动燃油泵、8 号线驱动 IDG、10 号线驱动液压泵、11 号线驱动润滑组件),同时起 动机通过 5 号线驱动高压转子、4 号线可人工转动高压转子,如图 4 所示。AGB 内部包含大 量齿轮和轴承等转动部件,这些部件通过发动机滑油润滑和冷却。润滑冷却过 AGB 的滑油通 过润滑组件中的回油泵抽吸至回油系统。AGB 内部齿轮线位号分布如下图所示。
三、故障分析
由统计可看出,AGB 导致的空停事件主要问题发生在 3 号线和 4 号线:
4 号线主 要问题表现为 N2 手摇驱动盖安装不当导致发动机后续运行过程中滑油渗漏,滑油渗漏导致 低滑油量/低滑油压力关车;
3 号线主要问题是 47 齿轮轴的滚棒轴承外轨道的螺柱因为高温 和高振动导致螺柱松动,和 AGB 壳体发生磨损产生大量铝质碎屑,金属屑堵塞回油滤导致油 滤旁通灯亮关车。
2009 年发动机厂家 CFM 发布 4 号线改装 SB72-0564,在该处增加碳封严的设计 以减少滑油渗漏,AGB 件号升级至 340-046-508-0。随着改装的执行,2020 年起未再发生该 类型的空停事件,该问题已基本得到解决。
2012 年发动机厂家 CFM 发布 3 号线改装 SB72-0879,将 47 齿轮轴的滚棒轴承 外轨道的固定形式,由螺柱+螺套+螺帽固定在 AGB 壳体上改成由螺栓+螺套固定到起动机驱 动盘上,以增强该处连接强度,AGB 件号升级至 340-046-509-0。目前在 3 号线位置上,件 号为 340-046-509-0 的最新构型 AGB 发生 2 起空停事件(分别为前述 2024 年 8 月空停事件和 2018 年 1 起空停事件),其他均为 340-046-508-0 及之前旧构型。全球 14000 多台 CFM56-7B 发动机中已有 12800 台执行了改装 SB72-0879。
四、近期案例
2024 年 8 月,国内 1 台 CFM56-7B 发动机空中滑油滤旁通灯点亮,导致发动机空停。地面检查发现 AGB 3 号线(驱动 EEC发电机)滚棒轴承外轨道的固定螺栓与起动机驱动盘发生严重磨损。
基本信息:发动机件号 CFM56-7B26,TSN=44376,CSN=23918,TSO=7309,CSO=4224,2020 年因更换寿命件送修;
AGB 件号 340-046-509-0,TSN=44376,CSN=23918,上次随发动机送修执行 改装 SB72-0879,改装后使用 7309FH/4224FC;
EEC 发电机转子件号 85465-2,TSN=44376,CSN=23918,无修理历史;
EEC 发电机静子件号 87006-9,TSN=12505,CSN=7130,TSR=7315,CSR=4229。
故障现象:空中滑油滤旁通灯点亮,机组收油门后灯未熄灭,机组关车。 排故发现:EEC 自测有故障代码 73-21271,EEC 发电机输送到 EEC 的电压超出范围;
AGB/TGB 磁堵含有大量磁性碎屑,检测含有部分 M50 轴承材料; 拆下 EEC 发电机,发现发电机转子和静子磨损严重,安装区域含有 大量金属屑,检测发现碎屑成分和磁堵类似; 拆下滑油回油滤和供油滤,检测发现含有大量铝质碎屑。
AGB 送修:AGB 送修分解发现 3 号线 47 齿轮轴滚棒轴承外轨道固定螺栓和螺套从起动 机驱动盘处脱出,起动机驱动盘螺栓安装处磨损严重,滚棒磨损 明显,其他部件无明显损伤。
厂家调查:发动机厂家 CFM 对 AGB 的 3 号线部件进行了失效分析并于 2025 年 5 月作出 了调查报告。调查认为 47 齿轮轴滚棒轴承外轨道与起动机驱动盘之间微小位移,导致轴承固定螺栓和螺套的振动,振动导致螺栓螺套和起动机驱动 盘之间的磨损,直到螺栓带着螺套从起动机驱动盘处脱出,磨损产生的金 属屑在回油滤堆积导致滑油滤旁通灯亮从而造成本次空停事件。从调查报 告结果看,本次新构型 AGB 3 号线失效模式与旧构型 AGB 基本相同,但根 据现有检测手段暂无法确定失效根本原因,本次调查关闭,但 CFMI 提到会 继续关注 AGB 的技术问题,以确定导致该失效模式的关键因素(单一或复合)。
五、厂家措施汇总
1、针对 4 号线 N2 手摇驱动盖漏油问题,发布改装 SB72-0564(2009)增加碳封严的设 计,AGB 件号升级至 340-046-508-0。
2、针对 3 号线滚棒轴承外轨道的螺柱松动磨损问题,发布 3 号线改装 SB72-0879(2012),将 47 齿轮轴的滚棒轴承外轨道的固定形式,由螺柱+螺套+螺帽固定在 AGB 壳体 上改成由 螺栓 +螺 套固定 到起动 机驱动盘 上 ,以增强 该处连接 强度, AGB 件号 升级至 340-046-509-0。
3、针对 EEC 发电机发布服务通告 SB73-0134(2017),以降低 EEC 发电机转子静子工 作温度和重量。
六、建议措施
1、随着改装 SB72-0564 的执行,4 号线 N2 手摇驱动盖漏油问题已基本得到解决。
2、2012 以来已有 12800 台 AGB 执行 3 号线改装 SB72-0879 升级成 340-046-509-0,仅 发生两起 3 号线问题导致的空停事件,概率较低。CFM 发布的 2024 年 8 月国内 AGB(件号 340-046-509-0)导致空停事件调查报告,目前尚无法确定根本原因,没有提供建议措施。
3、建议航司随部件送修或随发动机送修时执行改装 SB72-0879。
4、建议航司关注机队 EEC 发电机构型, 可考虑在翼将旧构型 EEC 发电机更换成SB73-0134 介绍的新构型,以减小 3 号线负荷。
5、建议航司当检查 AGB/TGB 磁堵或滑油滤发现铝屑时,除了执行手册中步骤拆下 EEC 发电机外,建议用孔探仪从冷却孔伸入 AGB 内腔检查 3 号线滚棒轴承外轨道固定螺柱/螺栓 的磨损情况。
6、建议航司评估针对 340-046-509-0 之前构型的 AGB 安装基座螺栓状态及松动迹象采 取一次性孔探检查的措施。注:2011 年 CFM WTTin Budapest 材料里提到孔探不是有效手段 发现此缺陷。
ISO-32-25-49876
部件信息:PN – 277A6000-562(轮毂PN:C20626200,赛峰着陆系统 / 轮胎PN:441Q09-1,固特异斜交轮胎),CSN:1,491 / 第五次轮胎更换和第一次OVHL。
最近Jejuair在对737-8主轮内半部分的扭矩臂销壳体进行首次大修时,发现了异常磨损。
磨损发生在孔周围,但一侧磨损明显更深,可能是由于扭矩臂销的移动或旋转导致的,详见附件。
所有9个壳体的直径都超过了CMM限制:最大0.5089英寸,需要提前进行衬套修理。
在某些情况下,即使经过车削后仍然存在单侧磨损,因此即使是在首次大修时也需要进行让步修理。
在737-800机队中,我们也发现了类似的磨损,但在大多数情况下是在第二次大修时发现的,当时车削和衬套修理是足够的。
我们怀疑根本原因可能是由于使用斜交轮胎导致的轮毂变形,目前正在与赛峰着陆系统讨论此事。